The formulation and manufacture of laundry and cleaning products is an area of ever-increasing complexity. The days of washing with soap and water are long behind us, and chemical suppliers continue to innovate with new materials designed to allow for colder washing, more energy efficient manufacture and the inclusion of more natural ingredients. With a vast range of raw materials at a formulator’s disposal it can feel overwhelming to know where to begin. This, along with our own determination to be a leading environmentally responsible manufacturer, drove us to develop our own guiding principles for responsible formulation chemistry.
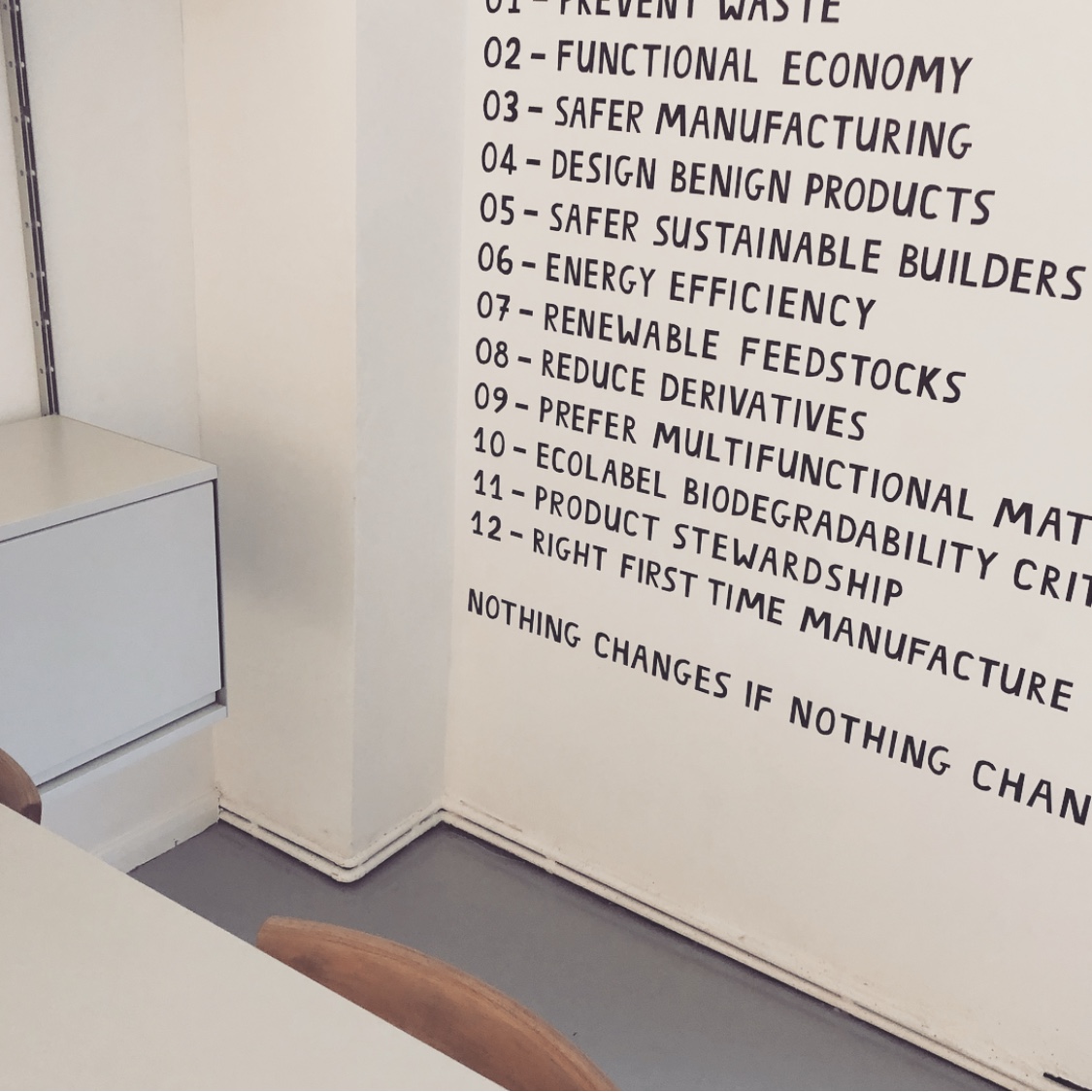
Twelve Guiding Principles
1 – Prevent Waste
Waste is a problem throughout the manufacturing industry, but particularly in chemical manufacturing where raw materials can carry hazards, meaning specialist disposal is required. The best solution to this issue is prevention. In limiting the range of raw materials we purchase, we are able to buy in bulk. This means we can buy in 1000 L returnable IBCs (intermediate bulk containers) rather than multiple 20 L drums. This is a model which we also always recommend to our customers where space and funds are available. We are then able to take back the empty IBC for washing and re-use.
When considering a new formulation, we start with the materials we know to have in stock already. This may limit the pool of available options but does help to focus in on the key requirements of a product. If we do decide that a new raw material is required, we always have the conversation with a supplier regarding packaging to try and limit waste as much as possible.
2 – Functional Economy
Functional economy is all about optimising performance. Trends are common in the cleaning industry. Over the last few years, we’ve seen enzymes, optical-brighteners, probiotics, encapsulated fragrances, and odour neutralisers to name a few. When we are approached by a supplier with a new raw material, our primary consideration is product performance over marketing.
This also applies retroactively. Over the last year we have removed opacifiers, dyes and functionally equivalent raw materials from several products. In all cases, these additions were providing style over substance and their removal can make room for other materials focused purely on benefiting performance.
3 – Safer Manufacturing
We manufacture all our products in our own factory in Finedon, Northamptonshire. All new and existing formulations must consider the health and safety of our factory workers. We regularly check updated summaries of classifications and labelling from ECHA (European Chemicals Agency) and the UK post-Brexit equivalent to ensure we are on top of any developments. Over the years this has led to us phasing out raw materials classified as suspected carcinogens, particularly fine, dusty powders, and unnecessary solvents. It often requires invention to work around these raw materials whilst maintaining performance, but it is always worth the effort.
4 – Design Benign Products
Safer manufacturing and raw materials lead to safer products. This must be balanced with performance. It is commonly said that a sharp knife is safer than a blunt knife and this is often true with chemical products too. For example, a professional dishwash liquid will almost always be corrosive due to the nature of its operation. Formulating a less concentrated product where twice the amount would be required for the expected performance would go against several of our other principles.
Wherever it is possible to reduce hazards without impacting performance we do take this approach – even if it requires a more novel approach to formulation.
5 – Safer Sustainable Builders
Builders are additional raw materials added to a detergent to improve performance. Builders are often effective ways of improving performance with efficient use of raw materials, however there are some builders we choose to avoid.
An example of a builder we have moved away from in recent years is products based on phosphates and phosphonates. These products are ubiquitous throughout the laundry industry but have been shown to contribute towards eutrophication – the over-enrichment of aquatic environments. This can lead to accelerated biological growth in rivers, lakes and reservoirs causing algae blooms and impacting other aquatic life.
We always take a cautious approach when introduced to new builders and will only include them if they provide a notable benefit to performance and do not introduce any negative environmental consequences.
6 – Energy Efficiency
There are two factors we consider with regards to energy efficiency: our storage of raw materials and the manufacturing process, and the energy consumption of raw material synthesis and their carriage.
Where possible we buy in raw materials that are fluid liquids or powders at room temperatures. Pastes and solid raw materials are often available at higher concentrations, however these need to be kept warm (occasionally at temperatures as high as 60 °C) and this is always energy intensive. This point has been in focus recently given increasing energy costs. This is a difficult balance, as purchasing materials at lower concentration lowers efficiency: we would much rather use 1 x 100% concentrated IBC than 2 x 50% concentrated where possible to reduce transport cost and carbon footprint.
An additional consideration is the origin of the raw material. Unfortunately, there is a lack of UK chemical manufacturers, but we do always buy from the UK or Europe before looking further afield wherever we can.
7 – Renewable Feedstocks
Surfactants and other raw materials can be derived from various sources depending on the product. These sources can be non-renewable (petroleum) or renewable (palm, coconut, castor seed, sugar beet, etc.). We formulate with this in mind to use renewably sourced raw materials and higher grade RSPO (Roundtable on Sustainable Palm Oil) or otherwise certified stock where available. Whilst using RSPO palm oil or other plant-derived surfactants does decrease dependency on petroleum they are not without their own issues. It could be argued that increased dependency on naturally derived chemicals leads to expanding plantations in areas that would otherwise contain rainforest, continued deforestation and a continued reduction in global biodiversity. This further drives our desire to reduce waste, only use what is functionally necessary for our products and continue to trial novel alternative surfactants that may help to ease future demand on palm and coconut whilst still avoiding ‘synthetic’/petroleum sources.
8 – Reduce Derivatives
Over time, with requests from various customers, it is easy to end up with a handful of similar formulations differing only in colour, fragrance, or very small performance differences. In line with our aims to prevent waste, we have tried to reduce our product range, only beginning a new formulation where there are distinct requirements which cannot be fulfilled by an existing product.
We have also driven to reduce raw material derivatives. By reducing our range of purchased materials, we can buy more efficiently and in greater bulk.
9 – Prefer Multifunctional Materials
Why use two raw materials when you can use one? Some raw materials can have multiple uses. An example of this would be sodium chloride. This is commonly used to bulk out powder detergents but can also be used in liquid laundry detergents and washing up liquids as a thickener. Amphoteric surfactants are another example as they help to increase detergency, whilst being very effective foam builders and good at lowering product irritancy. If we can use fewer raw materials per product without impacting performance, we will look to do so.
10 – Biodegradability Criteria
The biodegradability of cleaning products is of increasing concern. As of 2004 all surfactants sold within the EU need to pass a certain standard of biodegradability testing, so all suppliers generally meet this criterion for surfactants. This is not true of other raw materials.
We only want to use components that are biodegradable or readily biodegradable, or which don’t require biodegradability criteria, like salt. We do this regardless of whether the law says we need to. For example, acrylic polymers are still commonplace in powder dishwash formulations to reduce streaking and water marks, but we won’t use them. We are making changes all the time, updating old formulations to be in line with this vision and only making new products that fit the bill.
11 – Product Stewardship
Product stewardship is taking a holistic view of each product: considering all aspects from production, packaging, health and safety and more. It is about taking a balanced approach to formulation – not getting too focused on one individual aspect of the process but thinking of the product as a whole. Not easy to do – but when one aspect is prioritised above all else it can be to the overall detriment of the final product.
It is a benefit of being a small business with no more than 30 employees that we all know and take into consideration each other’s challenges. If we can work together during formulation to make a choice of packaging or health and safety procedure easier or more in-line with our principles, this is the approach we will try to take.
12 – Right First Time Manufacture
There will always be hiccoughs every now and again during production, but we try our best to formulate reliable, repeatable products. Before any new formulation reaches bulk production, it will be made at least three or four times in the lab and have undergone stability testing. This way we can avoid unexpected and expensive surprises during the first batch.
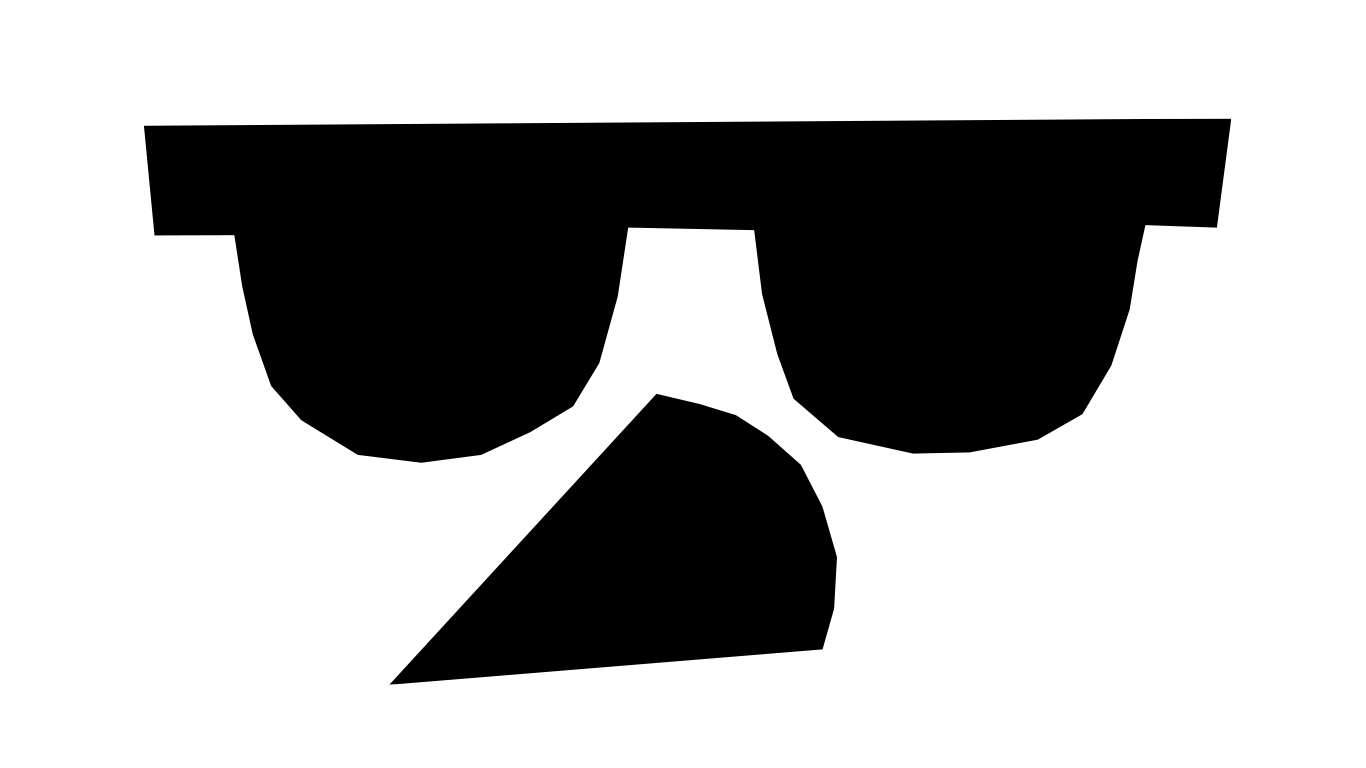
About This Series
We hope this has given you a glimpse into the difficult decisions we have to make whenever we encounter the need for a new formulation or product reformulation. This is part of a series of blogs about us, our products and our values. Keep checking back for more.